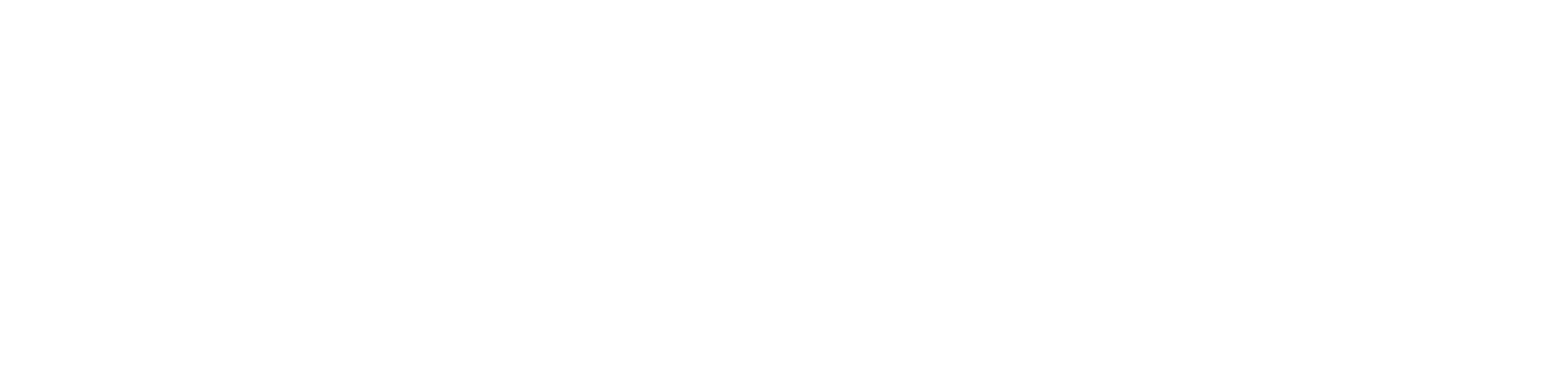
Erstmals vor 3500 Jahren von den Hethitern verwendet und seit der Antike in großem Maßstab hergestellt, versteht man unter Stählen Eisenwerkstoffe, die weniger als 2% Kohlenstoff enthalten.
Bei höheren Gehalten, wie sie etwa auch im Hochofen gewonnenes Roheisen aufweist, führt der Versuch einer Formänderung, etwa durch Schmieden, zum Bruch. Zur Stahlherstellung gehört demnach das Entfernen überschüssigen Kohlenstoffs, aber auch anderer unerwünschter Elemente aus dem Roheisen durch das sogenannte „Frischen“. Um 1860 geschah das noch vorwiegend händisch durch einen „Puddeln“ genannten Vorgang. Dabei wurden etwa 250 kg zuvor gegossener Roheisenblöcke in einem kleinen Ofen erneut geschmolzen. Zusätzlich wurde zerstoßenes Eisenerz beigegeben, das ebenfalls schmolz und auf dem flüssigen Eisen eine sauerstoffreiche Schlacke bildete. Wurde dieses Bad nun per Hand gerührt, konnte der Sauerstoff aus der Schlacke den Kohlenstoff im Roheisen zu Kohlendioxid verbrennen, wodurch das Bad zu kochen schien. Kohlenstoff in Eisen hat eine ähnliche Wirkung wie Salz in Wasser: er senkt den Schmelzpunkt. Mit der Zeit bildeten sich so feste, kohlenstoffarme Stahlklümpchen, an denen sich durch das Rühren und spätere Wälzen im Bad weitere Schichten anlagerten, deren Zusammensetzung in hohem Maße vom Geschick, der Erfahrung und der Kraft der Puddler abhing. Das Puddeln war harte Arbeit. Nicht nur galt es ständig die heiße Schmelze zu rühren und die Temperatur zu überwachen, die hohe Kunst lag darin, zu erkennen, ab wann sich fester Stahl abzuscheiden begann.
Durch das Puddeln konnte erstmals Stahl guter Qualität in großen Mengen hergestellt werden, der für Eisenbahnschienen, den Eiffelturm, die Freiheitsstatue und nicht zuletzt für Schusswaffen verwendet wurde. Den Preis dafür zahlten letztlich die akkordarbeitenden Puddler. In ihren 12 bis 16 Stunden dauernden Schichten hatten sie vier bis sechs Schmelzen zu schaffen und wenn eine misslang, musste sie wiederholt werden. Zusammen mit Hitze und Rauch der die Öfen befeuernden Steinkohle führte das dazu, dass die Puddler meist ihren vierzigsten Geburtstag nicht erlebten. So verwundert es nicht, dass das Puddeln bis 1880 fast vollständig durch automatisierte Verfahren ersetzt wurde, die auf günstigerem Weg größere Mengen homogeneren Stahls herstellen konnten.
Eines dieser Verfahren war das „Windfrischen“ in der Bessemerbirne, wobei heiße Luft von unten in das flüssige Roheisen eingeblasen wurde und der Luftsauerstoff den unerwünschten Kohlenstoff verbrannte. Da Luft aber zum Großteil aus Stickstoff besteht, löste sich auch dieser und machte Bessemer-Stahl spröde. Die Methode erlebte von 1880 bis 1890 eine kurze Blüte, trat aber zusehends in den Schatten des Siemens-Martin-Verfahrens, bei dem ein vorgeheiztes Gemisch aus Luft und Erdgas über die Schmelze geleitet wurde. Die so erzielten hohen Temperaturen erlaubten es auch große Mengen festen Einsatzes, wie Erz, Schrott oder Legierungsmittel beizugeben. Das Frischen geschah wie beim Puddeln durch den Kontakt zwischen flüssigem Roheisen und Schlacke, allerdings für bis zu 600 t auf einmal. Das benötigte zwar mit 8 bis 12 Stunden pro Schmelze deutlich mehr Zeit als eine Bessemerbirne, lieferte aber auch den besseren Stahl, weshalb bis 1960 der Großteil des weltweit produzierten Stahls so hergestellt wurde.
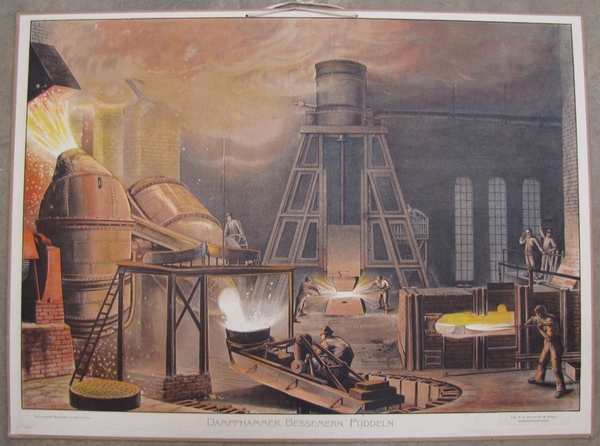
In der Ära des Siemens-Martin-Ofens entstanden auch die ersten legierten Stähle, denen man bewusst andere Elemente wie Mangan, Chrom oder Nickel zugab, um ihre Eigenschaften gezielt zu beeinflussen. Beginnend mit dem 1882 durch Robert Hadfield entwickelten „Mangalloy“, einem Mangan-Stahl, fanden diese Werkstoffe schnell Anklang. So verwendeten die Gebrüder Wright einen Chrom-Nickel-Stahl für ihr Flugzeug und Henry Ford ließ Vanadium-Stähle im Modell-T verbauen. 1912 schließlich brachten die Krupp-Werke den ersten rostfreien Chrom-Nickel-Stahl auf den Markt.
Heute stammen etwa zwei Drittel des weltweit produzierten Stahls aus einem Linz-Donawitz- oder kurz LD-Konverter. Wie die Bessemerbirne ist auch das 1949 entwickelte LD-Verfahren eine Form des Windfrischens. Allerdings wird nicht heiße Luft von unten, sondern reiner Sauerstoff von oben eingeblasen. Da dies weit aggressiver ist, müssen zusätzlich zum flüssigen Roheisen ca. 20 % Schrott zur Kühlung des Stahlbads zugegeben werden. Das LD-Verfahren konnte sich dennoch schnell durchsetzen, verband es doch die Flexibilität und die niedrigen Kosten des Bessemer-Verfahrens mit der hohen Qualität des Siemens-Martin-Ofens.
Seit den 1960er-Jahren gewann zudem die Sekundärmetallurgie an Bedeutung, bei der der gefrischte Stahl in einem eigenen Gefäß, der Pfanne, auf die gewünschte Zusammensetzung und Gießtemperatur gebracht wird. Ebenso kann der Stahl in der Pfanne einer Vakuumbehandlung unterzogen werden, um überschüssige Gase wie Stickstoff oder Sauerstoff zu entfernen. Moderne Hochleistungsstähle werden oftmals nach dem Gießen ein weiteres Mal unter Vakuum aufgeschmolzen und gereinigt, um höchste Qualität zu erzielen. Neben dem konventionellen Gießen von Blöcken oder Strängen gewinnt, speziell für Sonderanwendungen, das Zerstäuben der Schmelze zu feinsten Kügelchen für die Herstellung pulvermetallurgischer Stähle an Bedeutung.
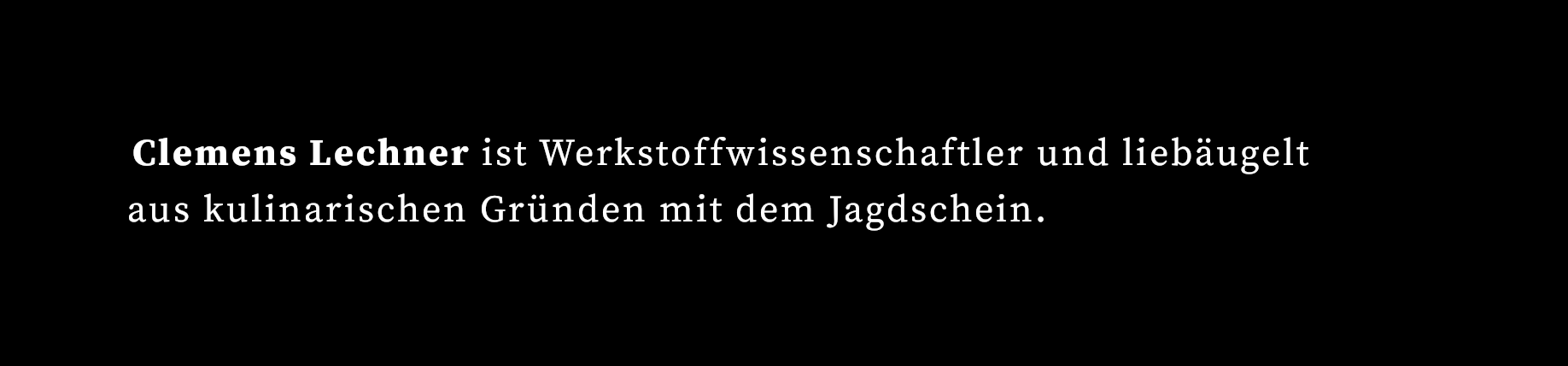
Durch all diese Verfahren unterscheiden sich heute produzierte Stähle in ihrem chemischen wie strukturellem Aufbau deutlich von Stählen früherer Epochen. Ihre hohe Reinheit verhindert, dass an einer Verunreinigung Risse entstehen können und durch gezieltes Legieren sind sie hart, fest und doch zäh genug, um auch bei dünneren Läufen Sicherheit zu garantieren. Weshalb moderne Waffen heute anders gestaltet werden können als noch vor 50, 100 oder 150 Jahren: Mit heutigen Materialien, hätte man wohl damals schon anders gebaut.
Text: Clemens Lechner
Bild oben: Technologische Wandtafel von Max Eschner aus den 1920er-Jahren mit der Darstellung einer Bessemerbirne links, einem Dampfhammer in der Mitte und dem Puddeln rechts; Vänersborgs museum (CC BY 4.0)